Create/Update Planning Routings
Use this screen to calculate planning routing records for end item parts.
On this screen, you select the parts and key resources you wish to generate planning routings for, using manufacturing bill of materials and routing information. After you enter the screen criteria, you can execute a process to identify key resource usage for each part, based on its routing and the routings of any subassemblies in its manufacturing bill of material.
For this process to execute successfully, you must first set up key resources and link the key resources to specific routing lines on the Manage Routings/Release Routings screens. On these screens, you identify the key resource that is consumed as well as the fixed and per-unit quantity that is consumed by this operation. The Fixed Usage quantity represents the amount consumed per order lot, regardless of the size of the order. The Unit Usage quantity indicates the quantity consumed for each unit produced.
Routing lines must be in effect as of the current date and must have a type code of Standard or Capacity Planning to be considered by the process. Alternate operations are not included in the calculation.
The Create/Update Planning Routings process takes key resource information for each selected part and looks through the preferred or other specified routing to determine the key resources used in the production of this part and how much of each key resource is consumed. In addition, for assembly parts, the process performs a full manufacturing bill of material explosion and search through the preferred or other specified routings for all effective parts in the BOM. Routings for phantom components are not included. The manufacturing bill of materials information is defined on the Manage Manufacturing Bills of Material/Release Manufacturing Bills of Material screens. For BOM explosion purposes, the current date is used as the effective date. Manufacturing BOM lines with configuration IDs are ignored. Reference and tool component parts are included for planning routing calculations.
The BOM component quantity type and quantity is used to calculate the appropriate unit usage quantity for routings linked to a component of the end item. If the Incl Scrap/Yield % in Planning Process check box is selected on the Configure Production Control Settings screen, part and BOM scrap and yield percentages are also applied to the calculations.
Key resource consumption for any components has a lead time offset calculated to determine when the key resource is consumed in relation to the end item's due date. This calculation is based on the lead time of any parent assemblies (including the end item). Manufacturing BOM lead time offsets are also considered.
Example
In the following illustration:
- The number inside each box represents that part's lead time; the number outside the box represents the lead time offset for that component.
- A planning routing line associated for key resource usage in part A's selected routing lines has a lead time offset of zero.
- A planning routing line for key resource in part B's routing would have a lead time offset of 9 days (10 {part A's lead time]-1 [BOM offset]).
- A routing line for part J would have a lead time offset of 36 days (10 [A] - 1 + 15 [B] - 2 + 15 [F] - 1).
- Note if subassembly F was a phantom component, the lead time offset would be 21 days (10 [A] - 1 + 15 [B] - 1).
- Note that if subassembly B was a phantom component, the lead time offset would be 22 days (10 [A] – 2 + 15 [F] -1)
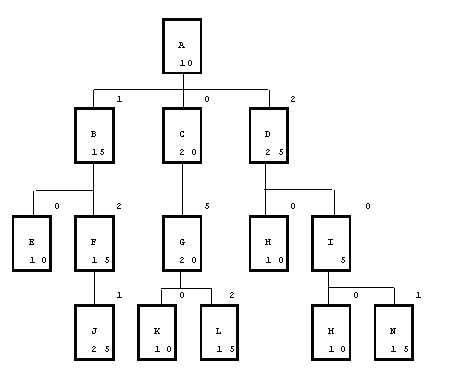
- Related Topics:
- Display the Create/Update Planning Routings Screen
You access the Create/Update Planning Routings screen from the Materials domain. - Contents of the Create/Update Planning Routings Screen
Use the fields and options to configure the Create/Update Planning Routings screen. - Table Information for the Create/Update Planning Routings Screen
Changes to the Create/Update Planning Routings screen update several tables.